ಕಳಪೆ ನೀರಿನ ಪ್ರತಿರೋಧ, ಅಸಮ ಮೇಲ್ಮೈ, ಹೆಚ್ಚಿನ ಪುಡಿ ಅಂಶ ಮತ್ತು ಅಸಮ ಉದ್ದ? ಜಲಚರ ಆಹಾರ ಉತ್ಪಾದನೆಯಲ್ಲಿ ಸಾಮಾನ್ಯ ಸಮಸ್ಯೆಗಳು ಮತ್ತು ಸುಧಾರಣಾ ಕ್ರಮಗಳು.
ನಮ್ಮ ದೈನಂದಿನ ಜಲಚರ ಆಹಾರ ಉತ್ಪಾದನೆಯಲ್ಲಿ, ನಾವು ವಿವಿಧ ಅಂಶಗಳಿಂದ ಕೆಲವು ಸಮಸ್ಯೆಗಳನ್ನು ಎದುರಿಸಿದ್ದೇವೆ. ಎಲ್ಲರೊಂದಿಗೆ ಚರ್ಚಿಸಲು ಕೆಲವು ಉದಾಹರಣೆಗಳು ಇಲ್ಲಿವೆ, ಅವುಗಳೆಂದರೆ:
1, ಸೂತ್ರ
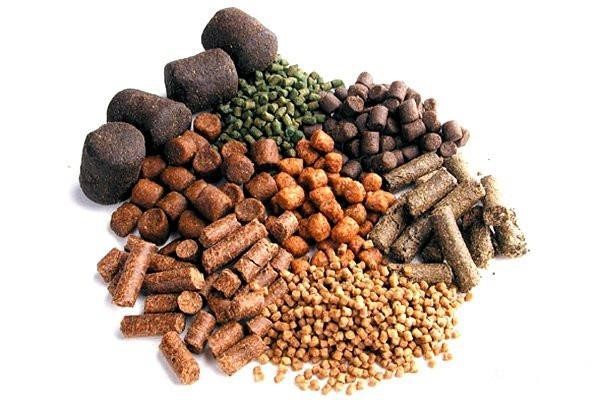
1. ಮೀನಿನ ಆಹಾರದ ಸೂತ್ರ ರಚನೆಯಲ್ಲಿ, ರಾಪ್ಸೀಡ್ ಮೀಲ್, ಹತ್ತಿ ಮೀಲ್, ಇತ್ಯಾದಿ ಕಚ್ಚಾ ನಾರಿಗೆ ಸೇರಿದ ಹೆಚ್ಚಿನ ರೀತಿಯ ಊಟದ ಕಚ್ಚಾ ವಸ್ತುಗಳಿವೆ. ಕೆಲವು ಎಣ್ಣೆ ಕಾರ್ಖಾನೆಗಳು ಸುಧಾರಿತ ತಂತ್ರಜ್ಞಾನವನ್ನು ಹೊಂದಿವೆ, ಮತ್ತು ಎಣ್ಣೆಯನ್ನು ಮೂಲತಃ ಬಹಳ ಕಡಿಮೆ ಅಂಶದೊಂದಿಗೆ ಒಣಗಿಸಿ ಹುರಿಯಲಾಗುತ್ತದೆ. ಇದಲ್ಲದೆ, ಈ ರೀತಿಯ ಕಚ್ಚಾ ವಸ್ತುಗಳು ಉತ್ಪಾದನೆಯಲ್ಲಿ ಸುಲಭವಾಗಿ ಹೀರಿಕೊಳ್ಳುವುದಿಲ್ಲ, ಇದು ಹರಳಾಗುವಿಕೆಯ ಮೇಲೆ ಹೆಚ್ಚಿನ ಪರಿಣಾಮ ಬೀರುತ್ತದೆ. ಇದರ ಜೊತೆಗೆ, ಹತ್ತಿ ಮೀಲ್ ಅನ್ನು ಪುಡಿಮಾಡುವುದು ಕಷ್ಟ, ಇದು ದಕ್ಷತೆಯ ಮೇಲೆ ಪರಿಣಾಮ ಬೀರುತ್ತದೆ.
2. ಪರಿಹಾರ: ರೇಪ್ಸೀಡ್ ಕೇಕ್ ಬಳಕೆಯನ್ನು ಹೆಚ್ಚಿಸಲಾಗಿದೆ ಮತ್ತು ಅಕ್ಕಿ ಹೊಟ್ಟು ಮುಂತಾದ ಉತ್ತಮ ಗುಣಮಟ್ಟದ ಸ್ಥಳೀಯ ಪದಾರ್ಥಗಳನ್ನು ಸೂತ್ರಕ್ಕೆ ಸೇರಿಸಲಾಗಿದೆ. ಹೆಚ್ಚುವರಿಯಾಗಿ, ಸೂತ್ರದ ಸರಿಸುಮಾರು 5-8% ರಷ್ಟಿರುವ ಗೋಧಿಯನ್ನು ಸೇರಿಸಲಾಗಿದೆ. ಹೊಂದಾಣಿಕೆಯ ಮೂಲಕ, 2009 ರಲ್ಲಿ ಗ್ರ್ಯಾನ್ಯುಲೇಷನ್ ಪರಿಣಾಮವು ತುಲನಾತ್ಮಕವಾಗಿ ಸೂಕ್ತವಾಗಿದೆ ಮತ್ತು ಪ್ರತಿ ಟನ್ಗೆ ಇಳುವರಿಯೂ ಹೆಚ್ಚಾಗಿದೆ. 2.5 ಮಿಮೀ ಕಣಗಳು 8-9 ಟನ್ಗಳ ನಡುವೆ ಇವೆ, ಹಿಂದಿನದಕ್ಕೆ ಹೋಲಿಸಿದರೆ ಸುಮಾರು 2 ಟನ್ಗಳ ಹೆಚ್ಚಳ. ಕಣಗಳ ನೋಟವು ಗಮನಾರ್ಹವಾಗಿ ಸುಧಾರಿಸಿದೆ.
ಇದರ ಜೊತೆಗೆ, ಹತ್ತಿಬೀಜದ ಹಿಟ್ಟಿನ ದಕ್ಷತೆಯನ್ನು ಸುಧಾರಿಸಲು, ನಾವು ಹತ್ತಿಬೀಜದ ಹಿಟ್ಟಿನೊಂದಿಗೆ ರಾಪ್ಸೀಡ್ ಹಿಟ್ಟಿನ ಮಿಶ್ರಣವನ್ನು 2:1 ಅನುಪಾತದಲ್ಲಿ ಬೆರೆಸಿ ಪುಡಿಮಾಡಿದೆವು. ಸುಧಾರಣೆಯ ನಂತರ, ಪುಡಿಮಾಡುವ ವೇಗವು ಮೂಲತಃ ರಾಪ್ಸೀಡ್ ಹಿಟ್ಟಿನ ಹಿಟ್ಟಿನ ಹಿಟ್ಟಿನ ವೇಗಕ್ಕೆ ಸಮನಾಗಿತ್ತು.
2, ಕಣಗಳ ಅಸಮ ಮೇಲ್ಮೈ
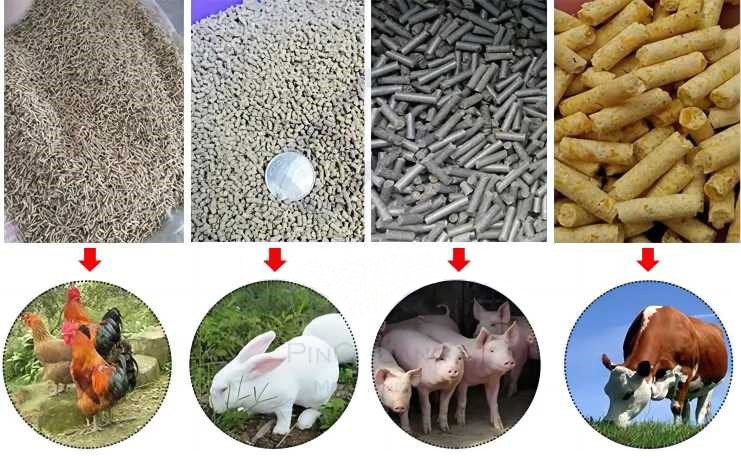
1. ಇದು ಸಿದ್ಧಪಡಿಸಿದ ಉತ್ಪನ್ನದ ಗೋಚರಿಸುವಿಕೆಯ ಮೇಲೆ ಹೆಚ್ಚಿನ ಪರಿಣಾಮ ಬೀರುತ್ತದೆ ಮತ್ತು ನೀರಿಗೆ ಸೇರಿಸಿದಾಗ, ಅದು ಕುಸಿಯುವ ಸಾಧ್ಯತೆಯಿದೆ ಮತ್ತು ಕಡಿಮೆ ಬಳಕೆಯ ದರವನ್ನು ಹೊಂದಿರುತ್ತದೆ. ಮುಖ್ಯ ಕಾರಣ:
(1) ಕಚ್ಚಾ ವಸ್ತುಗಳನ್ನು ತುಂಬಾ ಒರಟಾಗಿ ಪುಡಿಮಾಡಲಾಗುತ್ತದೆ ಮತ್ತು ಹದಗೊಳಿಸುವ ಪ್ರಕ್ರಿಯೆಯಲ್ಲಿ, ಅವು ಸಂಪೂರ್ಣವಾಗಿ ಪಕ್ವವಾಗುವುದಿಲ್ಲ ಮತ್ತು ಮೃದುವಾಗುವುದಿಲ್ಲ ಮತ್ತು ಅಚ್ಚು ರಂಧ್ರಗಳ ಮೂಲಕ ಹಾದುಹೋಗುವಾಗ ಇತರ ಕಚ್ಚಾ ವಸ್ತುಗಳೊಂದಿಗೆ ಚೆನ್ನಾಗಿ ಸಂಯೋಜಿಸಲಾಗುವುದಿಲ್ಲ.
(2) ಹೆಚ್ಚಿನ ಕಚ್ಚಾ ನಾರಿನ ಅಂಶವಿರುವ ಮೀನು ಆಹಾರ ಸೂತ್ರದಲ್ಲಿ, ಹದಗೊಳಿಸುವ ಪ್ರಕ್ರಿಯೆಯಲ್ಲಿ ಕಚ್ಚಾ ವಸ್ತುವಿನಲ್ಲಿ ಉಗಿ ಗುಳ್ಳೆಗಳು ಇರುವುದರಿಂದ, ಕಣಗಳ ಸಂಕೋಚನದ ಸಮಯದಲ್ಲಿ ಅಚ್ಚಿನ ಒಳಗೆ ಮತ್ತು ಹೊರಗೆ ಒತ್ತಡದ ವ್ಯತ್ಯಾಸದಿಂದಾಗಿ ಈ ಗುಳ್ಳೆಗಳು ಸಿಡಿಯುತ್ತವೆ, ಇದರ ಪರಿಣಾಮವಾಗಿ ಕಣಗಳ ಮೇಲ್ಮೈ ಅಸಮವಾಗಿರುತ್ತದೆ.
2. ನಿರ್ವಹಣಾ ಕ್ರಮಗಳು:
(1) ಪುಡಿಮಾಡುವ ಪ್ರಕ್ರಿಯೆಯನ್ನು ಸರಿಯಾಗಿ ನಿಯಂತ್ರಿಸಿ
ಪ್ರಸ್ತುತ, ಮೀನಿನ ಆಹಾರವನ್ನು ಉತ್ಪಾದಿಸುವಾಗ, ನಮ್ಮ ಕಂಪನಿಯು 1.2mm ಜರಡಿ ಮೈಕ್ರೋ ಪೌಡರ್ ಅನ್ನು ಬೃಹತ್ ಕಚ್ಚಾ ವಸ್ತುವಾಗಿ ಬಳಸುತ್ತದೆ. ಜರಡಿಯ ಬಳಕೆಯ ಆವರ್ತನ ಮತ್ತು ಸುತ್ತಿಗೆಯ ಉಡುಗೆಯ ಮಟ್ಟವನ್ನು ನಾವು ನಿಯಂತ್ರಿಸುತ್ತೇವೆ, ಇದರಿಂದಾಗಿ ಪುಡಿಮಾಡುವಿಕೆಯ ಸೂಕ್ಷ್ಮತೆಯನ್ನು ಖಚಿತಪಡಿಸಿಕೊಳ್ಳಬಹುದು.
(2) ಹಬೆಯ ಒತ್ತಡವನ್ನು ನಿಯಂತ್ರಿಸಿ
ಸೂತ್ರದ ಪ್ರಕಾರ, ಉತ್ಪಾದನೆಯ ಸಮಯದಲ್ಲಿ ಉಗಿ ಒತ್ತಡವನ್ನು ಸಮಂಜಸವಾಗಿ ಹೊಂದಿಸಿ, ಸಾಮಾನ್ಯವಾಗಿ 0.2 ರ ಸುತ್ತಲೂ ನಿಯಂತ್ರಿಸಿ. ಮೀನಿನ ಆಹಾರ ಸೂತ್ರದಲ್ಲಿ ಹೆಚ್ಚಿನ ಪ್ರಮಾಣದ ಒರಟಾದ ನಾರಿನ ಕಚ್ಚಾ ವಸ್ತುಗಳ ಕಾರಣ, ಉತ್ತಮ-ಗುಣಮಟ್ಟದ ಉಗಿ ಮತ್ತು ಸಮಂಜಸವಾದ ಹದಗೊಳಿಸುವ ಸಮಯ ಬೇಕಾಗುತ್ತದೆ.
3, ಕಣಗಳ ಕಳಪೆ ನೀರಿನ ಪ್ರತಿರೋಧ
1. ಈ ರೀತಿಯ ಸಮಸ್ಯೆ ನಮ್ಮ ದೈನಂದಿನ ಉತ್ಪಾದನೆಯಲ್ಲಿ ಅತ್ಯಂತ ಸಾಮಾನ್ಯವಾಗಿದೆ, ಸಾಮಾನ್ಯವಾಗಿ ಈ ಕೆಳಗಿನ ಅಂಶಗಳಿಗೆ ಸಂಬಂಧಿಸಿದೆ:
(1) ಕಡಿಮೆ ಹದಗೊಳಿಸುವ ಸಮಯ ಮತ್ತು ಕಡಿಮೆ ಹದಗೊಳಿಸುವ ತಾಪಮಾನವು ಅಸಮ ಅಥವಾ ಸಾಕಷ್ಟು ಹದಗೊಳಿಸುವಿಕೆ, ಕಡಿಮೆ ಮಾಗಿದ ಮಟ್ಟ ಮತ್ತು ಸಾಕಷ್ಟು ತೇವಾಂಶಕ್ಕೆ ಕಾರಣವಾಗುತ್ತದೆ.
(2) ಪಿಷ್ಟದಂತಹ ಅಂಟಿಕೊಳ್ಳುವ ವಸ್ತುಗಳ ಕೊರತೆ.
(3) ಉಂಗುರದ ಅಚ್ಚಿನ ಸಂಕೋಚನ ಅನುಪಾತವು ತುಂಬಾ ಕಡಿಮೆಯಾಗಿದೆ.
(4) ಸೂತ್ರದಲ್ಲಿ ಎಣ್ಣೆಯ ಅಂಶ ಮತ್ತು ಕಚ್ಚಾ ನಾರಿನ ಕಚ್ಚಾ ವಸ್ತುಗಳ ಪ್ರಮಾಣವು ತುಂಬಾ ಹೆಚ್ಚಾಗಿದೆ.
(5) ಪುಡಿಮಾಡುವ ಕಣ ಗಾತ್ರದ ಅಂಶ.
2. ನಿರ್ವಹಣಾ ಕ್ರಮಗಳು:
(1) ಉಗಿ ಗುಣಮಟ್ಟವನ್ನು ಸುಧಾರಿಸಿ, ನಿಯಂತ್ರಕದ ಬ್ಲೇಡ್ ಕೋನವನ್ನು ಹೊಂದಿಸಿ, ಹದಗೊಳಿಸುವ ಸಮಯವನ್ನು ವಿಸ್ತರಿಸಿ ಮತ್ತು ಕಚ್ಚಾ ವಸ್ತುಗಳ ತೇವಾಂಶವನ್ನು ಸೂಕ್ತವಾಗಿ ಹೆಚ್ಚಿಸಿ.
(2) ಸೂತ್ರವನ್ನು ಹೊಂದಿಸಿ, ಪಿಷ್ಟದ ಕಚ್ಚಾ ವಸ್ತುಗಳನ್ನು ಸೂಕ್ತವಾಗಿ ಹೆಚ್ಚಿಸಿ ಮತ್ತು ಕೊಬ್ಬು ಮತ್ತು ಕಚ್ಚಾ ನಾರಿನ ಕಚ್ಚಾ ವಸ್ತುಗಳ ಪ್ರಮಾಣವನ್ನು ಕಡಿಮೆ ಮಾಡಿ.
(3) ಅಗತ್ಯವಿದ್ದರೆ ಅಂಟು ಸೇರಿಸಿ. (ಸೋಡಿಯಂ ಆಧಾರಿತ ಬೆಂಟೋನೈಟ್ ಸ್ಲರಿ)
(4) ಸಂಕೋಚನ ಅನುಪಾತವನ್ನು ಸುಧಾರಿಸಿರಿಂಗ್ ಡೈ
(5) ಚೆನ್ನಾಗಿ ಪುಡಿಮಾಡುವುದರ ಸೂಕ್ಷ್ಮತೆಯನ್ನು ನಿಯಂತ್ರಿಸಿ
4, ಕಣಗಳಲ್ಲಿ ಅತಿಯಾದ ಪುಡಿ ಅಂಶ
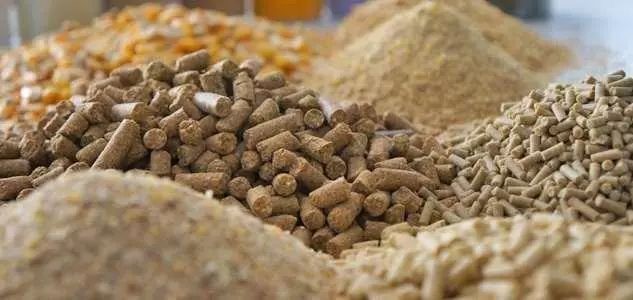
1. ತಂಪಾಗಿಸಿದ ನಂತರ ಮತ್ತು ಸ್ಕ್ರೀನಿಂಗ್ ಮಾಡುವ ಮೊದಲು ಸಾಮಾನ್ಯ ಪೆಲೆಟ್ ಫೀಡ್ ಕಾಣಿಸಿಕೊಳ್ಳುವುದನ್ನು ಖಚಿತಪಡಿಸಿಕೊಳ್ಳುವುದು ಕಷ್ಟ. ಪೆಲೆಟ್ಗಳಲ್ಲಿ ಹೆಚ್ಚು ಸೂಕ್ಷ್ಮ ಬೂದಿ ಮತ್ತು ಪುಡಿ ಇದೆ ಎಂದು ಗ್ರಾಹಕರು ವರದಿ ಮಾಡಿದ್ದಾರೆ. ಮೇಲಿನ ವಿಶ್ಲೇಷಣೆಯ ಆಧಾರದ ಮೇಲೆ, ಇದಕ್ಕೆ ಹಲವಾರು ಕಾರಣಗಳಿವೆ ಎಂದು ನಾನು ಭಾವಿಸುತ್ತೇನೆ:
A. ಕಣದ ಮೇಲ್ಮೈ ನಯವಾಗಿಲ್ಲ, ಛೇದನವು ಅಚ್ಚುಕಟ್ಟಾಗಿಲ್ಲ, ಮತ್ತು ಕಣಗಳು ಸಡಿಲವಾಗಿರುತ್ತವೆ ಮತ್ತು ಪುಡಿ ಉತ್ಪಾದನೆಗೆ ಗುರಿಯಾಗುತ್ತವೆ;
ಬಿ. ಪರದೆಯನ್ನು ಶ್ರೇಣೀಕರಿಸುವ ಮೂಲಕ ಅಪೂರ್ಣ ಸ್ಕ್ರೀನಿಂಗ್, ಮುಚ್ಚಿಹೋಗಿರುವ ಪರದೆಯ ಜಾಲರಿ, ರಬ್ಬರ್ ಚೆಂಡುಗಳ ತೀವ್ರ ಸವೆತ, ಹೊಂದಿಕೆಯಾಗದ ಪರದೆಯ ಜಾಲರಿಯ ದ್ಯುತಿರಂಧ್ರ, ಇತ್ಯಾದಿ;
ಸಿ. ಸಿದ್ಧಪಡಿಸಿದ ಉತ್ಪನ್ನದ ಗೋದಾಮಿನಲ್ಲಿ ಸಾಕಷ್ಟು ಉತ್ತಮವಾದ ಬೂದಿ ಶೇಷವಿದೆ, ಮತ್ತು ತೆರವು ಸಂಪೂರ್ಣವಾಗಿಲ್ಲ;
D. ಪ್ಯಾಕೇಜಿಂಗ್ ಮತ್ತು ತೂಕ ಮಾಡುವಾಗ ಧೂಳು ತೆಗೆಯುವಲ್ಲಿ ಅಪಾಯಗಳು ಅಡಗಿರುತ್ತವೆ;
ನಿರ್ವಹಣಾ ಕ್ರಮಗಳು:
A. ಸೂತ್ರ ರಚನೆಯನ್ನು ಅತ್ಯುತ್ತಮಗೊಳಿಸಿ, ರಿಂಗ್ ಡೈ ಅನ್ನು ಸಮಂಜಸವಾಗಿ ಆಯ್ಕೆಮಾಡಿ ಮತ್ತು ಸಂಕೋಚನ ಅನುಪಾತವನ್ನು ಚೆನ್ನಾಗಿ ನಿಯಂತ್ರಿಸಿ.
ಬಿ. ಗ್ರ್ಯಾನ್ಯುಲೇಷನ್ ಪ್ರಕ್ರಿಯೆಯಲ್ಲಿ, ಕಚ್ಚಾ ವಸ್ತುಗಳನ್ನು ಸಂಪೂರ್ಣವಾಗಿ ಹದಗೊಳಿಸಲು ಮತ್ತು ಮೃದುಗೊಳಿಸಲು ಟೆಂಪರಿಂಗ್ ಸಮಯ, ಆಹಾರದ ಪ್ರಮಾಣ ಮತ್ತು ಗ್ರ್ಯಾನ್ಯುಲೇಷನ್ ತಾಪಮಾನವನ್ನು ನಿಯಂತ್ರಿಸಿ.
C. ಕಣದ ಅಡ್ಡ-ಛೇದವು ಅಚ್ಚುಕಟ್ಟಾಗಿದೆ ಎಂದು ಖಚಿತಪಡಿಸಿಕೊಳ್ಳಿ ಮತ್ತು ಉಕ್ಕಿನ ಪಟ್ಟಿಯಿಂದ ಮಾಡಿದ ಮೃದುವಾದ ಕತ್ತರಿಸುವ ಚಾಕುವನ್ನು ಬಳಸಿ.
D. ಗ್ರೇಡಿಂಗ್ ಸ್ಕ್ರೀನ್ ಅನ್ನು ಹೊಂದಿಸಿ ಮತ್ತು ನಿರ್ವಹಿಸಿ, ಮತ್ತು ಸಮಂಜಸವಾದ ಸ್ಕ್ರೀನ್ ಕಾನ್ಫಿಗರೇಶನ್ ಬಳಸಿ.
ಇ. ಸಿದ್ಧಪಡಿಸಿದ ಉತ್ಪನ್ನ ಗೋದಾಮಿನ ಅಡಿಯಲ್ಲಿ ದ್ವಿತೀಯ ಸ್ಕ್ರೀನಿಂಗ್ ತಂತ್ರಜ್ಞಾನದ ಬಳಕೆಯು ಪುಡಿ ಅಂಶ ಅನುಪಾತವನ್ನು ಬಹಳವಾಗಿ ಕಡಿಮೆ ಮಾಡುತ್ತದೆ.
F. ಸಿದ್ಧಪಡಿಸಿದ ಉತ್ಪನ್ನದ ಗೋದಾಮು ಮತ್ತು ಸರ್ಕ್ಯೂಟ್ ಅನ್ನು ಸಮಯೋಚಿತವಾಗಿ ಸ್ವಚ್ಛಗೊಳಿಸುವುದು ಅವಶ್ಯಕ. ಇದರ ಜೊತೆಗೆ, ಪ್ಯಾಕೇಜಿಂಗ್ ಮತ್ತು ಧೂಳು ತೆಗೆಯುವ ಸಾಧನವನ್ನು ಸುಧಾರಿಸುವುದು ಅವಶ್ಯಕ. ಧೂಳು ತೆಗೆಯಲು ನಕಾರಾತ್ಮಕ ಒತ್ತಡವನ್ನು ಬಳಸುವುದು ಉತ್ತಮ, ಇದು ಹೆಚ್ಚು ಸೂಕ್ತವಾಗಿದೆ. ವಿಶೇಷವಾಗಿ ಪ್ಯಾಕೇಜಿಂಗ್ ಪ್ರಕ್ರಿಯೆಯ ಸಮಯದಲ್ಲಿ, ಪ್ಯಾಕೇಜಿಂಗ್ ಕೆಲಸಗಾರ ನಿಯಮಿತವಾಗಿ ಪ್ಯಾಕೇಜಿಂಗ್ ಸ್ಕೇಲ್ನ ಬಫರ್ ಹಾಪರ್ನಿಂದ ಧೂಳನ್ನು ಬಡಿದು ಸ್ವಚ್ಛಗೊಳಿಸಬೇಕು..
5, ಕಣದ ಉದ್ದ ಬದಲಾಗುತ್ತದೆ
1. ದೈನಂದಿನ ಉತ್ಪಾದನೆಯಲ್ಲಿ, ನಾವು ಸಾಮಾನ್ಯವಾಗಿ ನಿಯಂತ್ರಣದಲ್ಲಿ ತೊಂದರೆಗಳನ್ನು ಎದುರಿಸುತ್ತೇವೆ, ವಿಶೇಷವಾಗಿ 420 ಕ್ಕಿಂತ ಹೆಚ್ಚಿನ ಮಾದರಿಗಳಿಗೆ. ಇದಕ್ಕೆ ಕಾರಣಗಳನ್ನು ಸ್ಥೂಲವಾಗಿ ಈ ಕೆಳಗಿನಂತೆ ಸಂಕ್ಷೇಪಿಸಲಾಗಿದೆ:
(1) ಗ್ರ್ಯಾನ್ಯುಲೇಷನ್ಗೆ ಆಹಾರದ ಪ್ರಮಾಣವು ಅಸಮವಾಗಿದೆ ಮತ್ತು ಹದಗೊಳಿಸುವ ಪರಿಣಾಮವು ಬಹಳವಾಗಿ ಏರಿಳಿತಗೊಳ್ಳುತ್ತದೆ.
(2) ಅಚ್ಚು ರೋಲರುಗಳ ನಡುವಿನ ಅಸಮಂಜಸ ಅಂತರ ಅಥವಾ ರಿಂಗ್ ಅಚ್ಚು ಮತ್ತು ಒತ್ತಡದ ರೋಲರುಗಳ ತೀವ್ರ ಸವೆತ.
(3) ಉಂಗುರದ ಅಚ್ಚಿನ ಅಕ್ಷೀಯ ದಿಕ್ಕಿನಲ್ಲಿ, ಎರಡೂ ತುದಿಗಳಲ್ಲಿನ ವಿಸರ್ಜನಾ ವೇಗವು ಮಧ್ಯದಲ್ಲಿರುವುದಕ್ಕಿಂತ ಕಡಿಮೆಯಿರುತ್ತದೆ.
(4) ಉಂಗುರದ ಅಚ್ಚಿನ ಒತ್ತಡ ಕಡಿಮೆ ಮಾಡುವ ರಂಧ್ರವು ತುಂಬಾ ದೊಡ್ಡದಾಗಿದೆ ಮತ್ತು ತೆರೆಯುವಿಕೆಯ ಪ್ರಮಾಣವು ತುಂಬಾ ಹೆಚ್ಚಾಗಿದೆ.
(5) ಕತ್ತರಿಸುವ ಬ್ಲೇಡ್ನ ಸ್ಥಾನ ಮತ್ತು ಕೋನವು ಅಸಮಂಜಸವಾಗಿದೆ.
(6) ಗ್ರ್ಯಾನ್ಯುಲೇಷನ್ ತಾಪಮಾನ.
(7) ರಿಂಗ್ ಡೈ ಕಟಿಂಗ್ ಬ್ಲೇಡ್ನ ಪ್ರಕಾರ ಮತ್ತು ಪರಿಣಾಮಕಾರಿ ಎತ್ತರ (ಬ್ಲೇಡ್ ಅಗಲ, ಅಗಲ) ಪರಿಣಾಮ ಬೀರುತ್ತದೆ.
(8) ಅದೇ ಸಮಯದಲ್ಲಿ, ಸಂಕೋಚನ ಕೊಠಡಿಯೊಳಗೆ ಕಚ್ಚಾ ವಸ್ತುಗಳ ವಿತರಣೆಯು ಅಸಮವಾಗಿರುತ್ತದೆ.
2. ಫೀಡ್ ಮತ್ತು ಪೆಲೆಟ್ಗಳ ಗುಣಮಟ್ಟವನ್ನು ಸಾಮಾನ್ಯವಾಗಿ ಅವುಗಳ ಆಂತರಿಕ ಮತ್ತು ಬಾಹ್ಯ ಗುಣಗಳ ಆಧಾರದ ಮೇಲೆ ವಿಶ್ಲೇಷಿಸಲಾಗುತ್ತದೆ. ಉತ್ಪಾದನಾ ವ್ಯವಸ್ಥೆಯಾಗಿ, ನಾವು ಫೀಡ್ ಪೆಲೆಟ್ಗಳ ಬಾಹ್ಯ ಗುಣಮಟ್ಟಕ್ಕೆ ಸಂಬಂಧಿಸಿದ ವಿಷಯಗಳಿಗೆ ಹೆಚ್ಚು ಒಡ್ಡಿಕೊಳ್ಳುತ್ತೇವೆ. ಉತ್ಪಾದನಾ ದೃಷ್ಟಿಕೋನದಿಂದ, ಜಲವಾಸಿ ಫೀಡ್ ಪೆಲೆಟ್ಗಳ ಗುಣಮಟ್ಟದ ಮೇಲೆ ಪರಿಣಾಮ ಬೀರುವ ಅಂಶಗಳನ್ನು ಸ್ಥೂಲವಾಗಿ ಈ ಕೆಳಗಿನಂತೆ ಸಂಕ್ಷೇಪಿಸಬಹುದು:
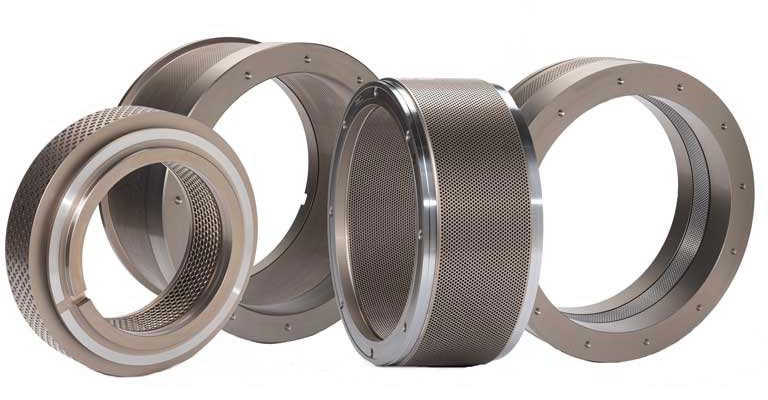
(1) ಸೂತ್ರಗಳ ವಿನ್ಯಾಸ ಮತ್ತು ಸಂಘಟನೆಯು ಜಲವಾಸಿ ಫೀಡ್ ಪೆಲೆಟ್ಗಳ ಗುಣಮಟ್ಟದ ಮೇಲೆ ನೇರ ಪರಿಣಾಮ ಬೀರುತ್ತದೆ, ಇದು ಒಟ್ಟು ಫೀಡ್ನ ಸರಿಸುಮಾರು 40% ರಷ್ಟಿದೆ;
(2) ಪುಡಿಮಾಡುವಿಕೆಯ ತೀವ್ರತೆ ಮತ್ತು ಕಣದ ಗಾತ್ರದ ಏಕರೂಪತೆ;
(3) ಉಂಗುರದ ಅಚ್ಚಿನ ವ್ಯಾಸ, ಸಂಕೋಚನ ಅನುಪಾತ ಮತ್ತು ರೇಖೀಯ ವೇಗವು ಕಣಗಳ ಉದ್ದ ಮತ್ತು ವ್ಯಾಸದ ಮೇಲೆ ಪರಿಣಾಮ ಬೀರುತ್ತದೆ;
(4) ಉಂಗುರದ ಅಚ್ಚಿನ ಸಂಕೋಚನ ಅನುಪಾತ, ರೇಖೀಯ ವೇಗ, ತಣಿಸುವಿಕೆ ಮತ್ತು ಹದಗೊಳಿಸುವಿಕೆಯ ಪರಿಣಾಮ ಮತ್ತು ಕಣಗಳ ಉದ್ದದ ಮೇಲೆ ಕತ್ತರಿಸುವ ಬ್ಲೇಡ್ನ ಪ್ರಭಾವ;
(5) ಕಚ್ಚಾ ವಸ್ತುಗಳ ತೇವಾಂಶ, ಹದಗೊಳಿಸುವ ಪರಿಣಾಮ, ತಂಪಾಗಿಸುವಿಕೆ ಮತ್ತು ಒಣಗಿಸುವಿಕೆಯು ಸಿದ್ಧಪಡಿಸಿದ ಉತ್ಪನ್ನಗಳ ತೇವಾಂಶ ಮತ್ತು ಗೋಚರಿಸುವಿಕೆಯ ಮೇಲೆ ಪರಿಣಾಮ ಬೀರುತ್ತದೆ;
(6) ಉಪಕರಣಗಳು, ಪ್ರಕ್ರಿಯೆಯ ಅಂಶಗಳು ಮತ್ತು ತಣಿಸುವ ಮತ್ತು ಹದಗೊಳಿಸುವ ಪರಿಣಾಮಗಳು ಕಣದ ಪುಡಿಯ ಅಂಶದ ಮೇಲೆ ಪರಿಣಾಮ ಬೀರುತ್ತವೆ;
3. ನಿರ್ವಹಣಾ ಕ್ರಮಗಳು:
(1) ಬಟ್ಟೆಯ ಸ್ಕ್ರಾಪರ್ನ ಉದ್ದ, ಅಗಲ ಮತ್ತು ಕೋನವನ್ನು ಹೊಂದಿಸಿ ಮತ್ತು ಸವೆದ ಸ್ಕ್ರಾಪರ್ ಅನ್ನು ಬದಲಾಯಿಸಿ.
(2) ಕಡಿಮೆ ಪ್ರಮಾಣದ ಆಹಾರದ ಕಾರಣದಿಂದಾಗಿ ಉತ್ಪಾದನೆಯ ಆರಂಭದಲ್ಲಿ ಮತ್ತು ಕೊನೆಯಲ್ಲಿ ಕತ್ತರಿಸುವ ಬ್ಲೇಡ್ನ ಸ್ಥಾನವನ್ನು ಸಮಯೋಚಿತವಾಗಿ ಹೊಂದಿಸಲು ಗಮನ ಕೊಡಿ.
(3) ಉತ್ಪಾದನಾ ಪ್ರಕ್ರಿಯೆಯಲ್ಲಿ, ಸ್ಥಿರವಾದ ಆಹಾರ ದರ ಮತ್ತು ಉಗಿ ಪೂರೈಕೆಯನ್ನು ಖಚಿತಪಡಿಸಿಕೊಳ್ಳಿ. ಉಗಿ ಒತ್ತಡ ಕಡಿಮೆಯಿದ್ದರೆ ಮತ್ತು ತಾಪಮಾನವು ಹೆಚ್ಚಾಗಲು ಸಾಧ್ಯವಾಗದಿದ್ದರೆ, ಅದನ್ನು ಸಮಯೋಚಿತವಾಗಿ ಸರಿಹೊಂದಿಸಬೇಕು ಅಥವಾ ನಿಲ್ಲಿಸಬೇಕು.
(4) ನಡುವಿನ ಅಂತರವನ್ನು ಸಮಂಜಸವಾಗಿ ಹೊಂದಿಸಿರೋಲರ್ ಶೆಲ್. ಹೊಸ ರೋಲರುಗಳೊಂದಿಗೆ ಹೊಸ ಅಚ್ಚನ್ನು ಅನುಸರಿಸಿ, ಮತ್ತು ಸವೆತದಿಂದಾಗಿ ಒತ್ತಡದ ರೋಲರ್ ಮತ್ತು ರಿಂಗ್ ಅಚ್ಚಿನ ಅಸಮ ಮೇಲ್ಮೈಯನ್ನು ತಕ್ಷಣ ಸರಿಪಡಿಸಿ.
(5) ರಿಂಗ್ ಅಚ್ಚಿನ ಮಾರ್ಗದರ್ಶಿ ರಂಧ್ರವನ್ನು ದುರಸ್ತಿ ಮಾಡಿ ಮತ್ತು ನಿರ್ಬಂಧಿಸಲಾದ ಅಚ್ಚು ರಂಧ್ರವನ್ನು ತಕ್ಷಣ ಸ್ವಚ್ಛಗೊಳಿಸಿ.
(6) ಉಂಗುರದ ಅಚ್ಚನ್ನು ಆದೇಶಿಸುವಾಗ, ಮೂಲ ಉಂಗುರದ ಅಚ್ಚಿನ ಅಕ್ಷೀಯ ದಿಕ್ಕಿನ ಎರಡೂ ತುದಿಗಳಲ್ಲಿರುವ ಮೂರು ಸಾಲುಗಳ ರಂಧ್ರಗಳ ಸಂಕೋಚನ ಅನುಪಾತವು ಮಧ್ಯದಲ್ಲಿರುವುದಕ್ಕಿಂತ 1-2 ಮಿಮೀ ಚಿಕ್ಕದಾಗಿರಬಹುದು.
(7) ಸಾಧ್ಯವಾದಷ್ಟು ತೀಕ್ಷ್ಣವಾದ ಅಂಚನ್ನು ಖಚಿತಪಡಿಸಿಕೊಳ್ಳಲು, 0.5-1 ಮಿಮೀ ದಪ್ಪವನ್ನು ನಿಯಂತ್ರಿಸುವ ಮೃದುವಾದ ಕತ್ತರಿಸುವ ಚಾಕುವನ್ನು ಬಳಸಿ, ಇದರಿಂದ ಅದು ಉಂಗುರದ ಅಚ್ಚು ಮತ್ತು ಒತ್ತಡದ ರೋಲರ್ ನಡುವಿನ ಮೆಶಿಂಗ್ ಲೈನ್ನಲ್ಲಿರುತ್ತದೆ.
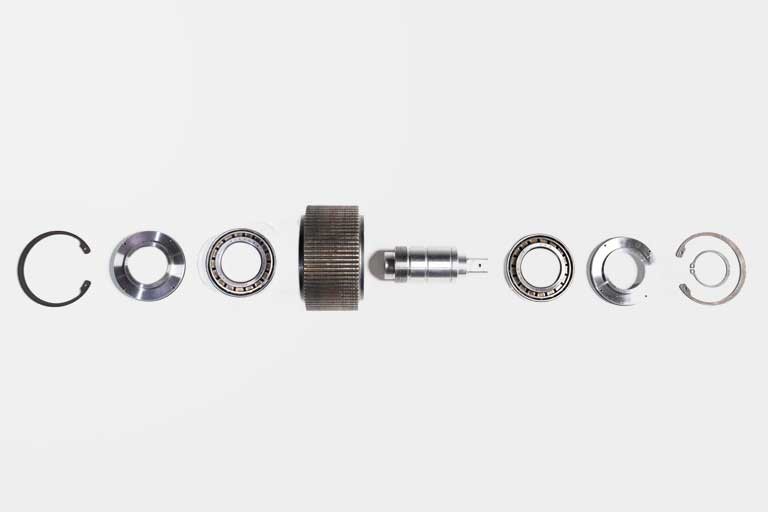
(8) ಉಂಗುರದ ಅಚ್ಚಿನ ಏಕಾಗ್ರತೆಯನ್ನು ಖಚಿತಪಡಿಸಿಕೊಳ್ಳಿ, ಗ್ರ್ಯಾನ್ಯುಲೇಟರ್ನ ಸ್ಪಿಂಡಲ್ ಕ್ಲಿಯರೆನ್ಸ್ ಅನ್ನು ನಿಯಮಿತವಾಗಿ ಪರಿಶೀಲಿಸಿ ಮತ್ತು ಅಗತ್ಯವಿದ್ದರೆ ಅದನ್ನು ಹೊಂದಿಸಿ.
6, ಸಾರಾಂಶ ನಿಯಂತ್ರಣ ಅಂಶಗಳು:
1. ರುಬ್ಬುವುದು: ನಿರ್ದಿಷ್ಟತೆಯ ಅವಶ್ಯಕತೆಗಳಿಗೆ ಅನುಗುಣವಾಗಿ ರುಬ್ಬುವಿಕೆಯ ಸೂಕ್ಷ್ಮತೆಯನ್ನು ನಿಯಂತ್ರಿಸಬೇಕು.
2. ಮಿಶ್ರಣ: ಸೂಕ್ತವಾದ ಮಿಶ್ರಣ ಪ್ರಮಾಣ, ಮಿಶ್ರಣ ಸಮಯ, ತೇವಾಂಶ ಮತ್ತು ತಾಪಮಾನವನ್ನು ಖಚಿತಪಡಿಸಿಕೊಳ್ಳಲು ಕಚ್ಚಾ ವಸ್ತುಗಳ ಮಿಶ್ರಣದ ಏಕರೂಪತೆಯನ್ನು ನಿಯಂತ್ರಿಸಬೇಕು.
3. ಪಕ್ವತೆ: ಪಫಿಂಗ್ ಯಂತ್ರದ ಒತ್ತಡ, ತಾಪಮಾನ ಮತ್ತು ತೇವಾಂಶವನ್ನು ನಿಯಂತ್ರಿಸಬೇಕು.
ಕಣ ವಸ್ತುವಿನ ಗಾತ್ರ ಮತ್ತು ಆಕಾರ: ಕಂಪ್ರೆಷನ್ ಅಚ್ಚುಗಳು ಮತ್ತು ಕತ್ತರಿಸುವ ಬ್ಲೇಡ್ಗಳ ಸೂಕ್ತ ವಿಶೇಷಣಗಳನ್ನು ಆಯ್ಕೆ ಮಾಡಬೇಕು.
5. ಸಿದ್ಧಪಡಿಸಿದ ಮೇವಿನಲ್ಲಿ ನೀರಿನ ಅಂಶ: ಒಣಗಿಸುವ ಮತ್ತು ತಂಪಾಗಿಸುವ ಸಮಯ ಮತ್ತು ತಾಪಮಾನವನ್ನು ಖಚಿತಪಡಿಸಿಕೊಳ್ಳುವುದು ಅವಶ್ಯಕ.
6. ಎಣ್ಣೆ ಸಿಂಪರಣೆ: ಎಣ್ಣೆ ಸಿಂಪರಣೆಯ ನಿಖರವಾದ ಪ್ರಮಾಣ, ನಳಿಕೆಗಳ ಸಂಖ್ಯೆ ಮತ್ತು ಎಣ್ಣೆಯ ಗುಣಮಟ್ಟವನ್ನು ನಿಯಂತ್ರಿಸುವುದು ಅವಶ್ಯಕ.
7. ಸ್ಕ್ರೀನಿಂಗ್: ವಸ್ತುವಿನ ವಿಶೇಷಣಗಳ ಪ್ರಕಾರ ಜರಡಿಯ ಗಾತ್ರವನ್ನು ಆಯ್ಕೆಮಾಡಿ.
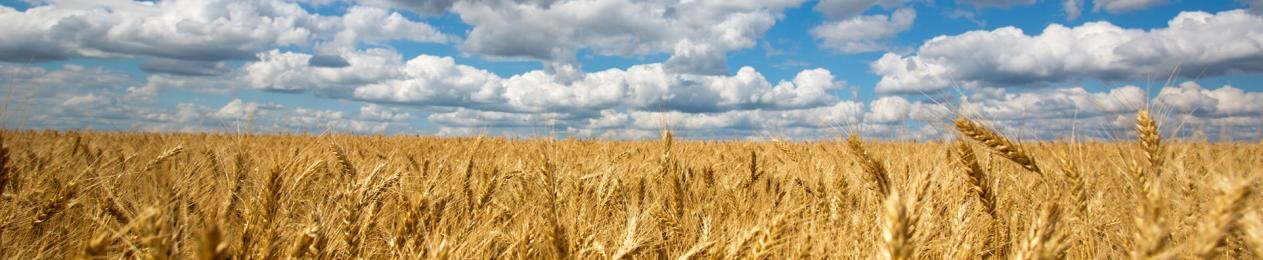
ಪೋಸ್ಟ್ ಸಮಯ: ನವೆಂಬರ್-30-2023